How DPR Rodgers successfully navigated Target Value Design for Atrium Health
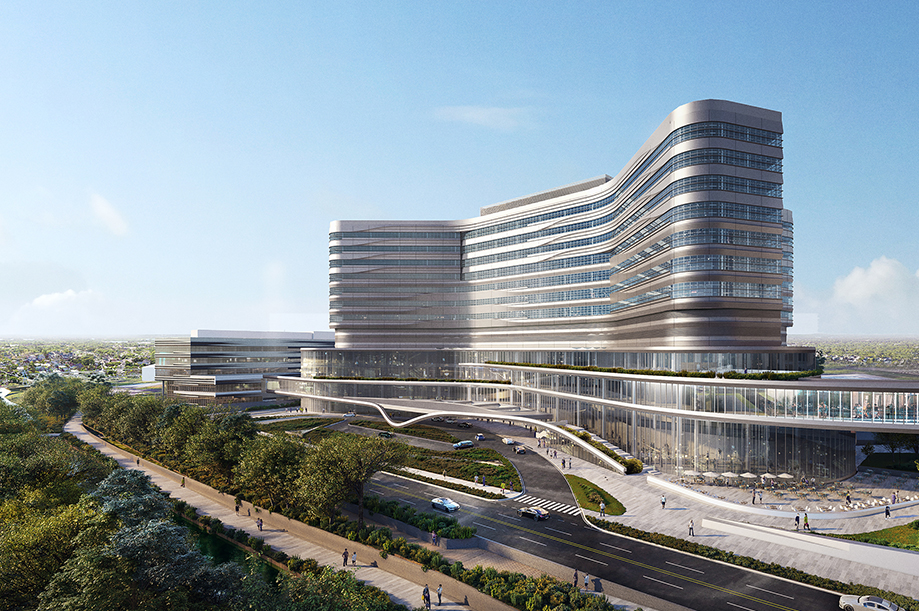
Target Value Design (TVD), the process of designing towards a budget without sacrificing quality or extending schedules, is increasingly popular with owners. TVD works when everyone involved in a project is part of the process. It requires true collaboration, transparency, rapid estimating, and rapid decision-making.
Challenge: Current tools created chaos for TVD delivery
Atrium Health embarked on a massive $650 million project involving the construction of a new rehabilitation hospital and an acute care bed tower at the Atrium Carolinas Medical Center (CMC) campus. To manage this undertaking, Atrium enlisted the help of DPR Rodgers (a joint venture of DPR Construction and Rodgers Builders), along with NBBJ and WSP. Preconstruction planning for these projects took place separately.
The team initially tackled the $100 million rehabilitation hospital project. Over nearly 10 months, approximately 30 people from various groups collaborated on this project. However, using their existing tools to track project costs, budgets, and timelines quickly led to chaos. Multiple users working on the same tracking log resulted in file overwrites, lost items, and duplications. Additionally, tracking items affecting multiple building systems became challenging.
Solution: Join – the collaborative project delivery platform
To address the chaotic decision-making process, DPR Rodgers sought an alternative solution. They required a platform that met specific criteria:
- Intuitive: Given the diverse technical skills of the users, the solution had to be user-friendly and easy to learn, even for non-technical stakeholders.
- Automated Tracking: The ideal solution needed to automate tracking and document every decision, including who entered items and when.
- Sortable: The ability to filter and sort data was crucial, especially for identifying pending decisions.
- Decision Impact: Transparency in tracking decision creators, pricing inputs, and the impact of each decision was essential.
- Visibility: Ensuring visibility for all cluster groups was challenging, so the solution had to improve cross-cluster communication.
- Fast Implementation: With project kick-off approaching, DPR Rodgers needed a solution that could be quickly implemented.
Join Checks All the Boxes for TVD
The Join platform fulfilled these criteria. The TVD team tested Join rigorously, loading estimates and cost items into the platform. “Due to the complexity and scale of the project, accurate cost tracking was critical. We couldn’t risk losing data or having miscalculations, so whatever software the team selected had to be correct. I tried to break Join, trying every possible way to mess it up,” said Melanie Moreschi, Healthcare Core Market Leader of DPR Construction.
After a 30-45 minute training session, the team found Join user-friendly and embraced its capabilities. “Most of the people were excited to try it once they realized how user-friendly it was and that they didn’t need to be an Excel or Smartsheet wizard to use it,” Melanie said.
TVD with Join: Real-Time Decision-Making
As with the rehab project, the Atrium Bed Tower TVD team consisted of 30+ people working in cluster groups, including the owner’s group, design team, and contractors. Estimators unfamiliar with TVD initially had concerns about switching to a new platform, but they adapted quickly. They liked the ability to restrict access to cost and quantity changes where needed. They also had the flexibility to note rough order of magnitude costs when a specific design wasn’t known; they could include allowances where appropriate for unknown items pending design confirmation.
Join streamlined the decision-making process, enabling real-time updates and tracking. It allowed DPR Rodgers and other groups to see the full impact of every decision, including indirect costs. Join’s transparency improved trust among project stakeholders. “Join allows us to provide that information in real-time, to give the owner the real estimate today – right now, not a minute from now,” added Melanie.
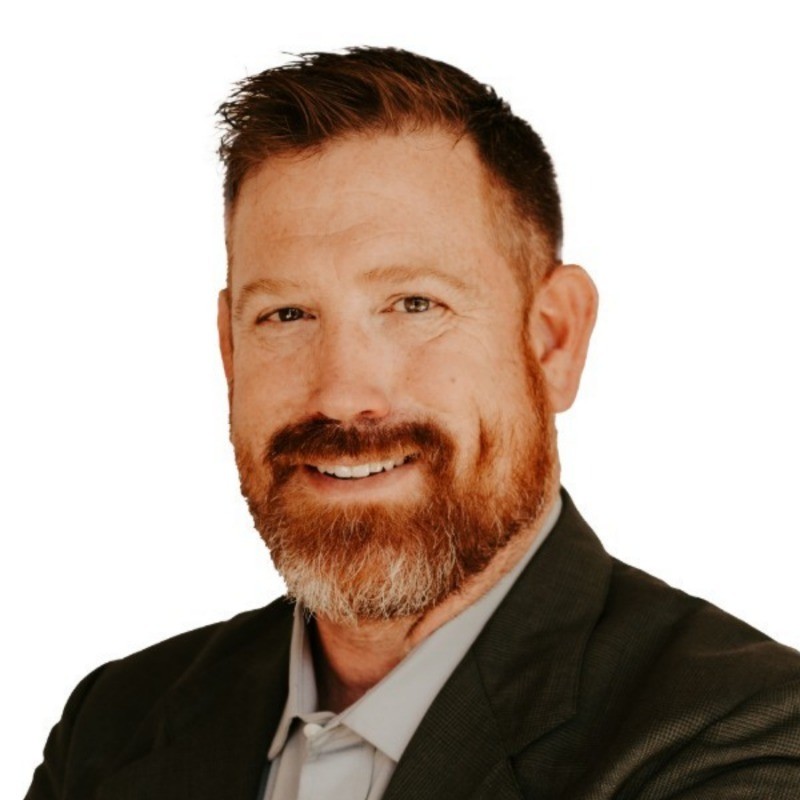
I have worked with several projects and have seen different methods for tracking decision-making during construction. Compared to those, I would say that Join is very intuitive. I like how it breaks down into individual items that can be reviewed and how it sends out messages to different teammates to say, “Hey, we put something in Join. Come check it out.
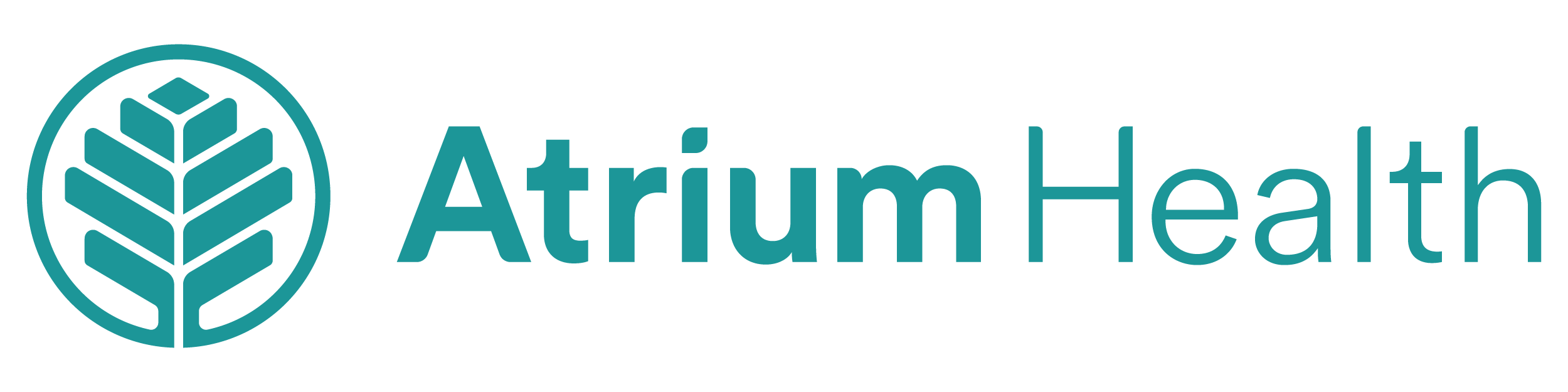
Director, Atrium Health
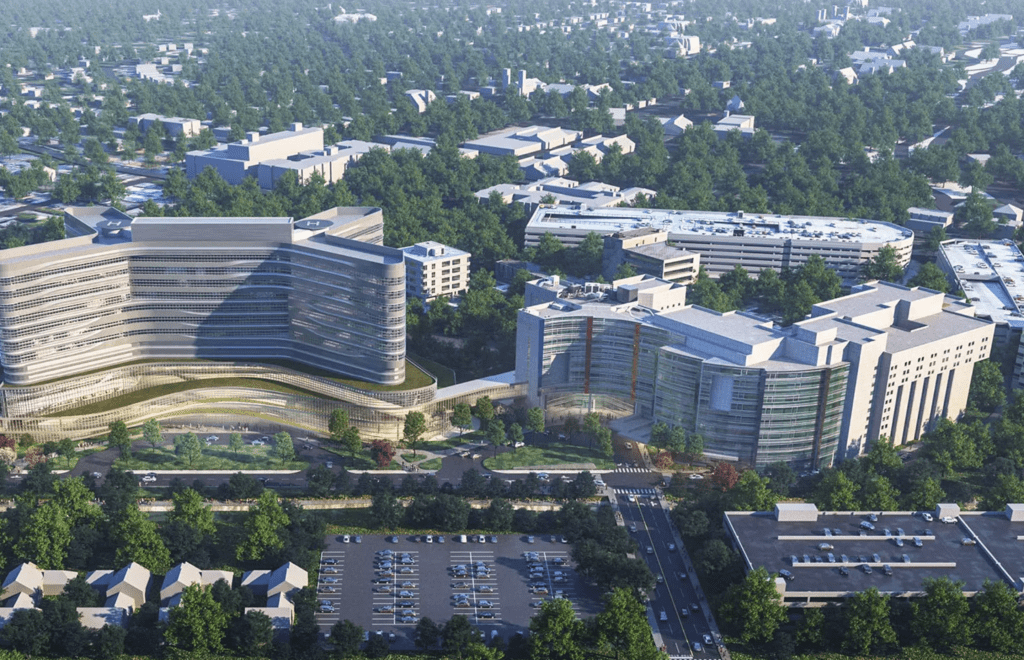
Impact: Enhanced Collaboration and Efficiency
Join facilitated efficient communication among cluster groups by using simple tags, such as @architect, to notify team members of actions taken. This improved pricing accuracy and allowed the owner to see direct construction costs and indirect cost impacts.
By providing a single source of truth and tracking decisions in real-time, Join streamlined communications and reduced the time spent on decision-making. It enabled scenario planning, helping teams assess the impact of decisions on their clusters.
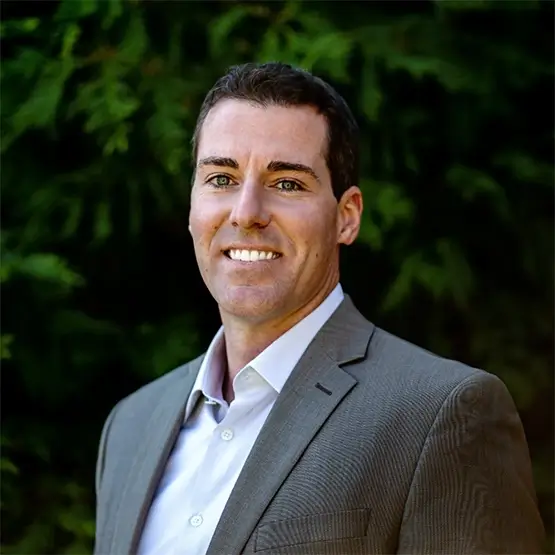
“What we’ve used in the past were traditional spreadsheet files, which were kind of scary at times. What I like about Join is it’s web-based. Anyone can go into it. It’s live. There’s no, ‘Hey, this is an old version’ or the formula isn’t working correctly.. The fact that Join is automated leaves very little opportunity for human error. It puts up guardrails to prevent someone like me from breaking formula links and miscalculating totals.”
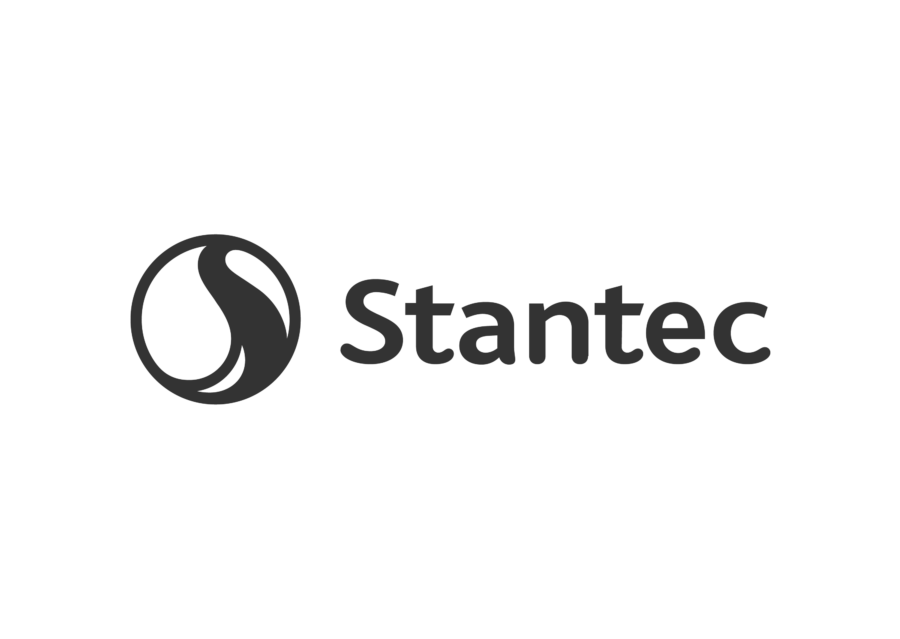
— Tyler Campbell, Stantec
More Accurate Pricing Moves the Project Right Along
Before Join, three to four people would have been working on a file that was shared periodically. By the time the “latest file” was sent, the info was likely outdated. With Join, all members with the proper permissions could see the current data — what was accepted and rejected — important information for project stakeholders.
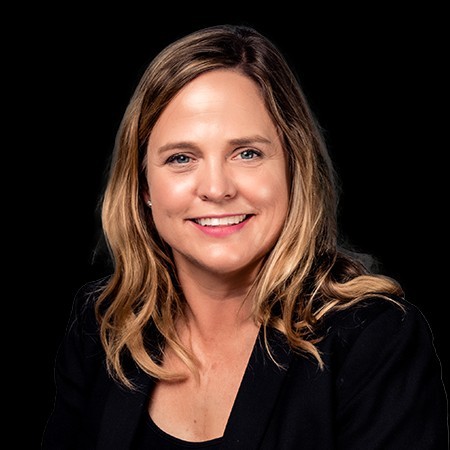
“Without Join, we would’ve spent more time getting to where we are now. I think it saved time, and it’s definitely saved money. My only regret is that we didn’t use it earlier in the process.”
Healthcare Core Market Leader
Melanie tracked the progress by getting a snapshot estimate every two weeks. “It allowed me to see where we were flatlining, if we were headed in the right direction. At one point,” she said, “there was a long, flat period where our estimate was not trending up or down, and that was an indicator that we had a decision problem. In August, we ended up with over 100 items that needed decisions, so we scheduled a full Join meeting day with the entire team. We reviewed every open Join item and identified next steps (action item, responsible person, and date required) to keep moving forward.”
From Melanie’s perspective, Join was critical for decision-making for all parties involved in the Atrium project. Without Join, Melanie said they might not have realized how many items depended on various decisions, which would have slowed the design process even more. Karl Schantz of NBBJ agrees: “Compared to the spreadsheets and other cost tracking tools we have seen, Join makes it much easier to navigate target value design. It’s nice to see the industry come to this maturity point, the point where we’re asking ourselves hard questions and making decisions in a smart and thoughtful way.”
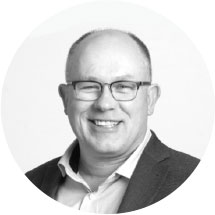
“If you’re working on an IPD or TVD project, Join is super helpful. I liked the ability to tie the drawings to the items so you can see exactly what was priced. Having everyone in the same easy-to-find location works really well. In many cases, the ability to leave comments and have the history is better than having the A3s or A4s because it’s right there with the number and the data.”
NBBJ