How Wohlsen got students into the classroom by fall & beat budget on Bucknell University’s first modular project
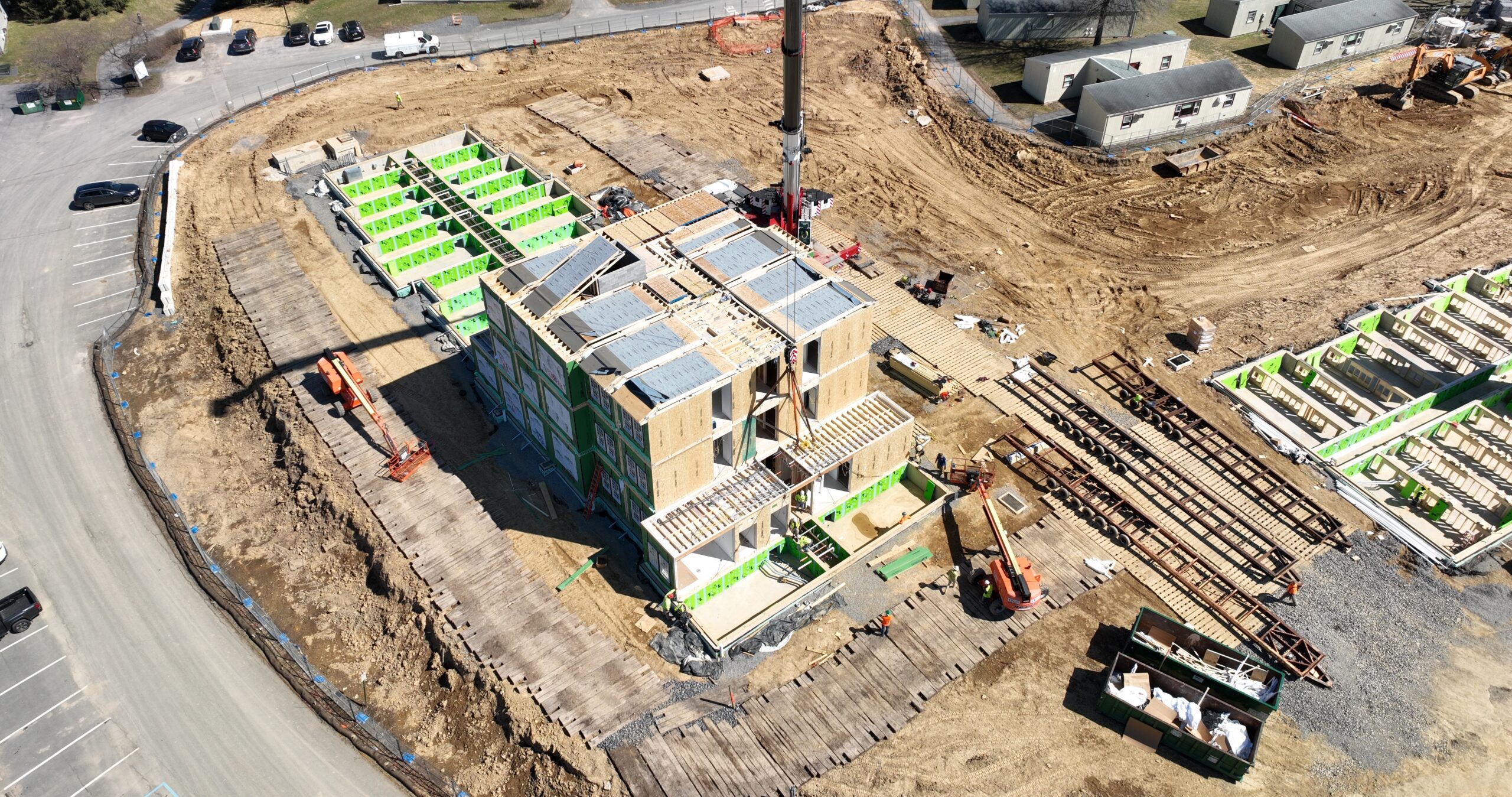
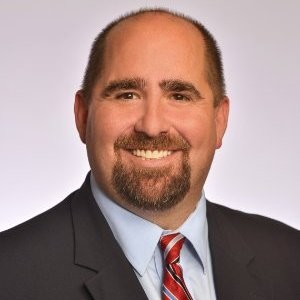
We were able to beat the budget that the owner wanted — and we have a happy client.
We were able to beat the budget that the owner wanted — and we have a happy client.
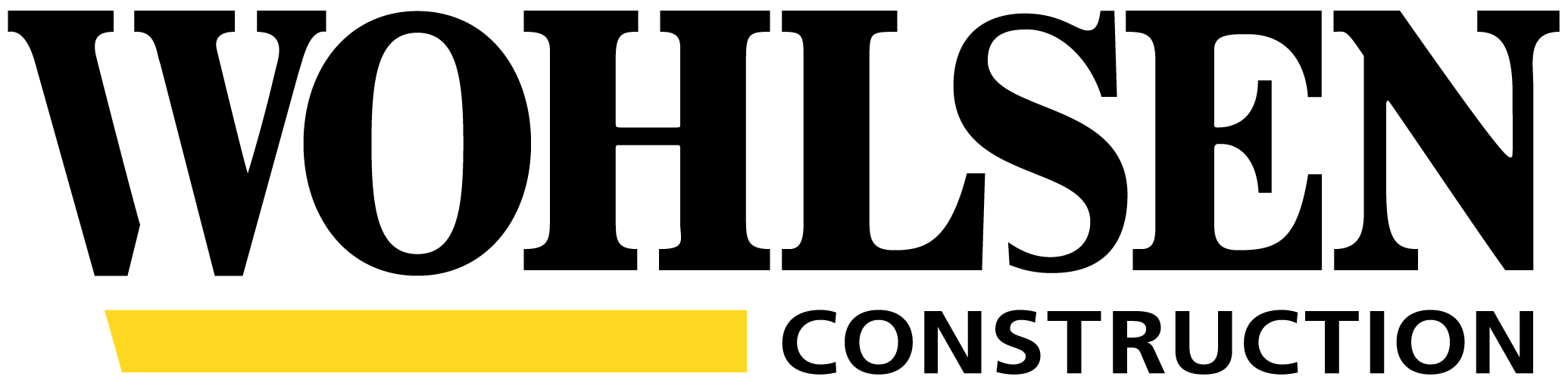
Vice President of Preconstruction and Estimating
Table of Contents
- Challenge: High stakes, tight deadline for owner’s first modular construction project
- Solution: Speed and stakeholder transparency with Join
- Impact: An exceptional client experience
- Fast onboarding and implementation
- Transparent decision tracking among multiple stakeholders
- GMP achieved in less than 3 months
- Tool for lean construction
- Consistent – and consistently positive – owner experience
Challenge: High stakes, tight deadline for owner’s first modular construction project
Bucknell University, a liberal arts university with approximately 3,700 students in the heart of Pennsylvania, embarked on a two-phase, two-year project to replace an existing 50-year-old student housing complex with four new LEED-certified residence halls. Gensler was awarded the contract for architecture and design, while Wohlsen was brought on board for preconstruction and construction management services.
Phase one included demolition of existing housing; construction of two three-story halls, each with 70 beds in an apartment setting; and installation of a geothermal heating/cooling system and infrastructure to help Bucknell achieve carbon neutrality by 2030.
The deadline? Everything needed to be move-in ready within eight months, for students arriving to start their fall semester. (The two remaining residence halls, as well as parking and an expanded outdoor recreation area, would be completed the following year as part of phase two.)
Wohlsen didn’t have time for a long, drawn-out preconstruction process and needed to get to a Guaranteed Maximum Price (GMP) fast. It was clear the team’s current toolkit wouldn’t work for the Bucknell project.
“Throughout the years, we went through so many different iterations of trying to visually communicate cost changes and other information about our clients’ projects through Excel, through PowerPoints, through various charts and graphs,” said Ed McCauley, Vice President of Innovation at Wohlsen. “We found that there was very little consistency across the board in how we captured, tracked, and reported on changes.”
Adding another layer of complexity: This was Bucknell’s first modular construction project, so it was critical for the Wohlsen team to quickly but thoroughly identify, assess, and agree on decisions with the owner as well as the Gensler design team, the modular contractor, and others. While modular construction offers obvious cost and productivity benefits – Bucknell was able to reduce the time-to-completion schedule by a year – it requires overcoming unique challenges in design, manufacturing, technology, logistics, assembly, and so much more across the entire project lifecycle.
For Wohlsen, it was essentially one preconstruction, purchasing, and planning effort applied to all four residence halls, since nearly every building component was identical. One uninformed decision or unanticipated expense could multiply exponentially and blow the entire project budget.
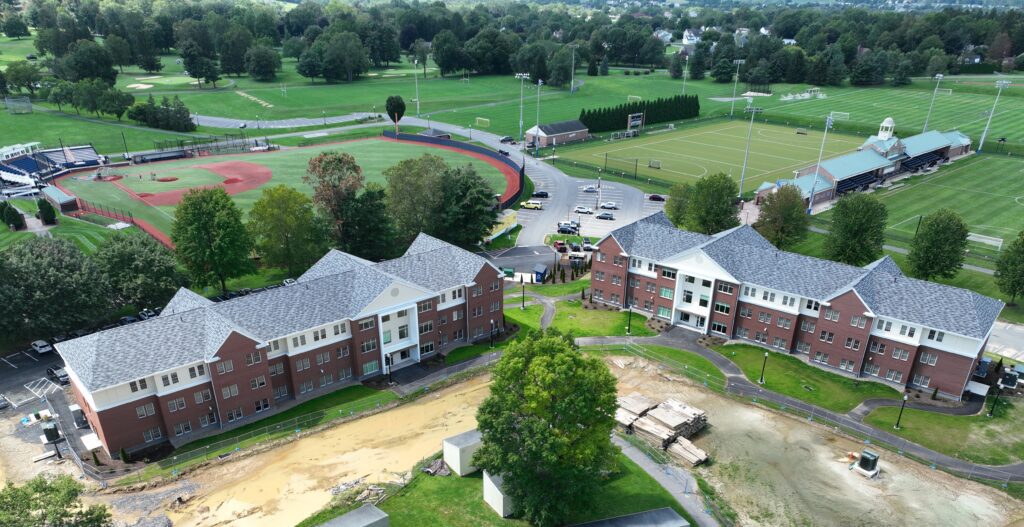
Solution: Speed and Stakeholder Transparency With Join
It all boiled down to providing a superior experience for stakeholders. This included ensuring that decisions were made transparently, communication was easy and efficient, risks were minimized, opportunities were leveraged, and a successful outcome was achieved. Join was the clear solution.
“With our former system that just presented numbers and line items, it was really tough to visualize and communicate,” said Bob Liberato, Vice President of Preconstruction and Estimating at Wohlsen. “Join appealed to us right away because we saw it as a decision-making tool. It lets us inform owners and designers of options, and we use the platform to work together on educated decisions to drive the project forward as quickly as possible.”
Fast Onboarding and Implementation
The timeframe it takes to bring a project through preconstruction wasn’t the only concern. Wohlsen was worried about onboarding and how long it would take to use Join. After all, Wohlsen had rolled out other popular construction software in the past and knew how challenging an onboarding process could be.
As head of innovation, Ed is involved in the discovery and review processes for Wohlsen’s software implementations. One of his priorities is making sure the technology is easy for users to adopt and integrate it into their daily workflows. Join easily met that expectation. “It doesn’t matter if you’re a seasoned preconstruction manager or you’re just starting that journey,” said Ed. “You’ve got a tool to help facilitate conversations, which ultimately makes it a much easier process for the client.”
With the help of Join’s sales and onboarding teams, Wohlsen was not only able to implement and use Join in near-record time – it got to GMP in less than three months.
“We use the platform to work together on educated decisions to drive the project forward as quickly as possible”
Bob Liberato, Vice President of Preconstruction and Estimating
Transparent Decision Tracking Among Multiple Stakeholders
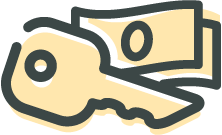
Bucknell University (Owner)
When you’re the owner making heavy-stakes decisions, it’s imperative to be able to analyze the data affecting those decisions. Join’s clear, real-time data visualizations allowed Bucknell to quickly understand decision impact, building trust and confidence.
“You can look at the data in multiple dimensions, slice-and-dice and look at it from different directions. Bucknell just wanted to see information presented in the most simple way possible, and Join represented that,” said Ed.
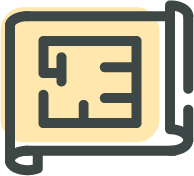
Gensler (Design)
Join’s centralized, detailed knowledge base allows designers to optimize costs and improve communication while maintaining the overall design vision – increasing decision clarity among all stakeholders.
“Within Join, we can see the comments people made, decisions that were made, and what and when drawings and documents were revised,” said Bob. “[On the Bucknell project], it helped us collaborate on solutions and also validate that what came out of the design documents matched what we agreed to do. Having that history is huge.”
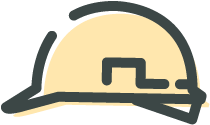
Modular Fabrication Contractor:
Typical of modular construction, most of the fabrication was done off-site by the modular vendor, resulting in an extra layer of planning and coordination.
“Part of it is taking a lot of time to understand what’s being done off-site versus on-site,” said Dan Millard, the Wohlsen preconstruction manager on the project. “Since there was so much work being done off-site, we had to have a place to track anything that changed with the modular vendor and how that would impact the site. Join was instrumental in helping us keep track of the ins and outs.”
In one specific instance, there were three manufacturers to choose from for the halls’ standard elevator and a decision needed to be made quickly. Wohlsen recommended one manufacturer that would save Bucknell $82,000, but the university had an existing master contract for campus-wide elevator maintenance from another manufacturer. Could Bucknell confirm if the company would service other manufacturers’ products, or negotiate an exception for the new residence halls? There were also questions about how the recommended elevator would affect electrical capacity, as well as the modular vendor’s design. And, of course, any design changes needed to be cleared by the Gensler team, as well.
Without Join, this issue would have likely required multiple calls, meetings, spreadsheets, and more. And all these activities likely would not have been captured in a single location, where someone could quickly go back and investigate what was the background for the decision.
With Join, “we presented the options, tracked comments and discussions from multiple project members, and came together on a decision, all within days,” said Dan. “And we saved quite a bit of money.”
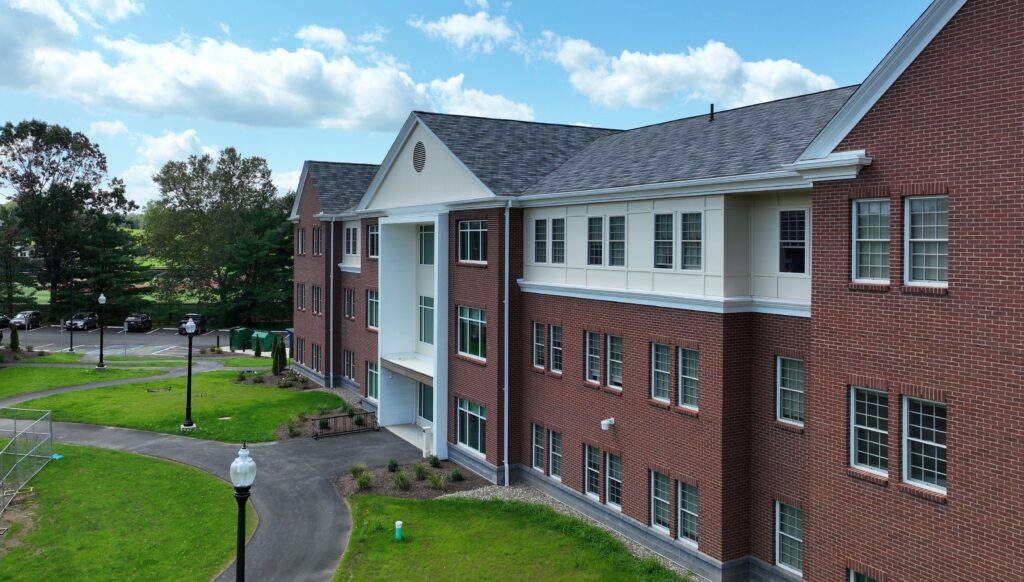
Impact: An Exceptional Client Experience
GMP Achieved in Less Than 3 Months
With Join, the team was able to fully implement the software and get to a GMP within three months. This was no small feat for a multi-year project, especially during a time when inflation and an uncertain global economy remained hot-button concerns.
Wohlsen was able to transform complex, ever-changing project data into clear, real-time visualizations that allowed stakeholders to quickly understand when decisions were made and how they impacted the overall budget. Said Dan: “Join’s dashboard is powerful: ‘This is where we’re at compared to where you want to be.’ And it’s very straightforward. It’s a visual, a picture, that’s easy to understand and communicate.”
Put simply: “We were able to get the project to beat the budget that the owner wanted,” said Bob. “And we have a happy client.”
“We presented the options, tracked comments and discussions from multiple project members, and came together on a decision, all within days. And we saved quite a bit of money.”
Dan Millard, Preconstruction Manager, Wohlsen Construction
Tool for Lean Construction
Dan, who is CM-Lean certified, is a big advocate for adopting Lean construction principles, including standardizing work processes, implementing continuous improvement methods, and reducing waste (such as wasted time). Dan sees Join as a vital digital tool for Lean construction, from enhancing visual communication to tracking and visualizing workflows.
Visual communication is a foundational approach among Lean project team members as they update plans, schedule activities, analyze and discuss problems, and track key performance indicators. Using Join to bolster visual communication and to execute other aspects of Lean was a no-brainer for Dan.
“You’re trying to optimize the whole project and involve all the stakeholders with Lean, so there are a lot of parallels between a good Lean project and target value delivery with Join,” he said. “The Bucknell project has become somewhat of a poster child because of our use of the Last Planner System and visual communication.”
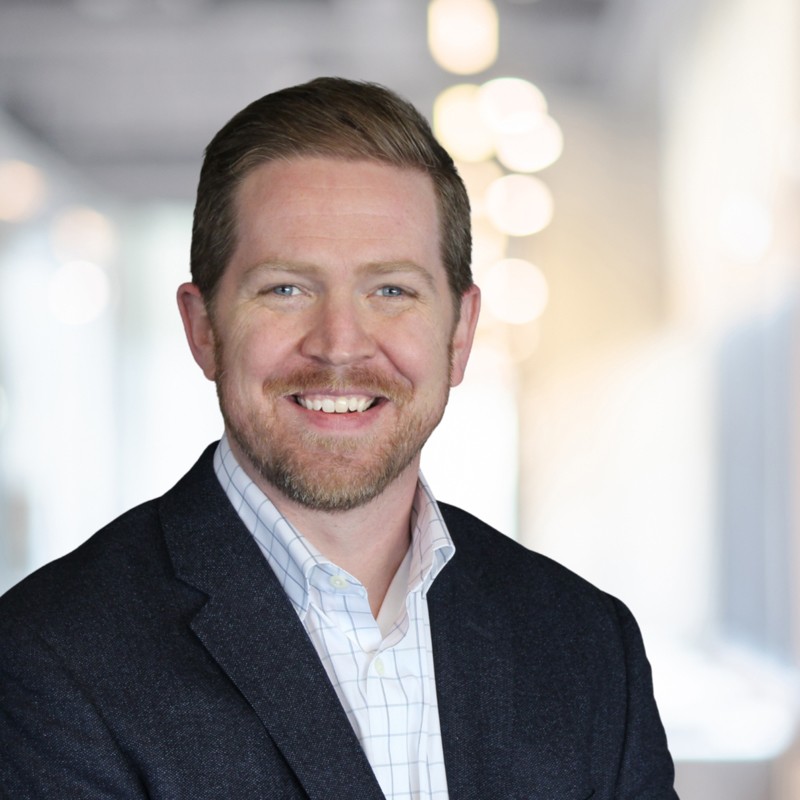
Join offers a strong and consistent experience for the owner throughout the process, hands-down.
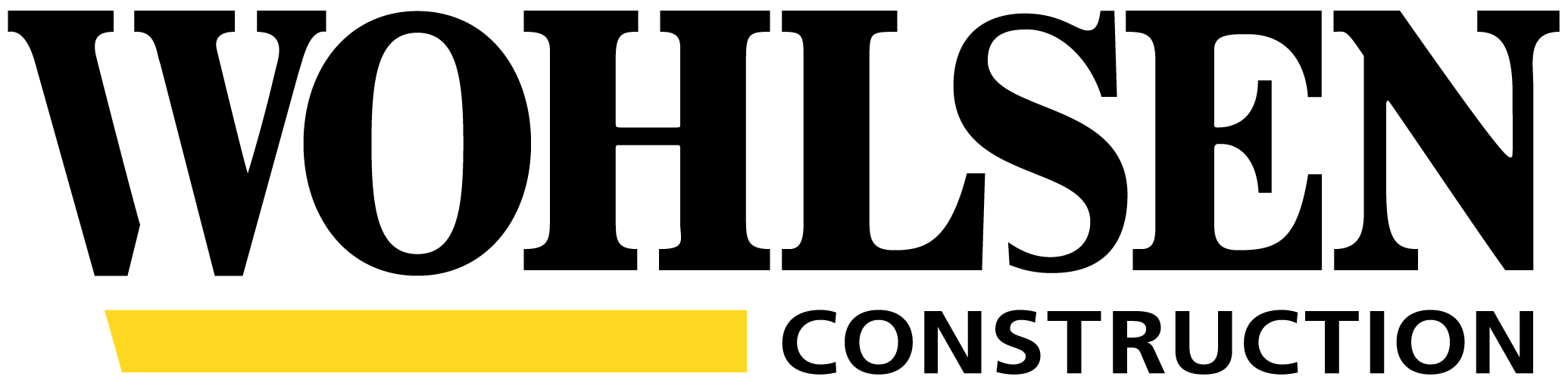
Vice President of Innovation
Consistent – and Consistently Positive – Owner Experience
The client experience begins at the first meeting and first interview. For Wohlsen, Join helped the team set a positive impression with Bucknell and demonstrate innovation in construction technology from the very beginning.
“Join offers a strong and consistent experience for the owner throughout the process, hands-down,” said Ed. “The way we start the relationship with the client sets the tone for the rest of the project – being able to really create an environment that’s going to help them have the best experience. It becomes a very easy sales pitch at that point. Join was the obvious tool to do that job and really improved that experience for our clients. You could see the value proposition immediately.”
That experience and the trust built over the course of their partnership is opening up other opportunities for Wohlsen at the university. Aside from phase two of the resident halls project, with construction beginning December 2023, Bucknell has turned to Wohlsen to advise them on the earliest stages of other housing construction. “We have a chance to prove ourselves, and if they’re able to negotiate it, we’re going to put our best foot forward and Join’s going to be part of that,” said Bob.
“Join was the obvious tool to do the job and really improved that experience for our clients. You could see the value proposition immediately.”
Bob Liberato, Vice President of Preconstruction and Estimating
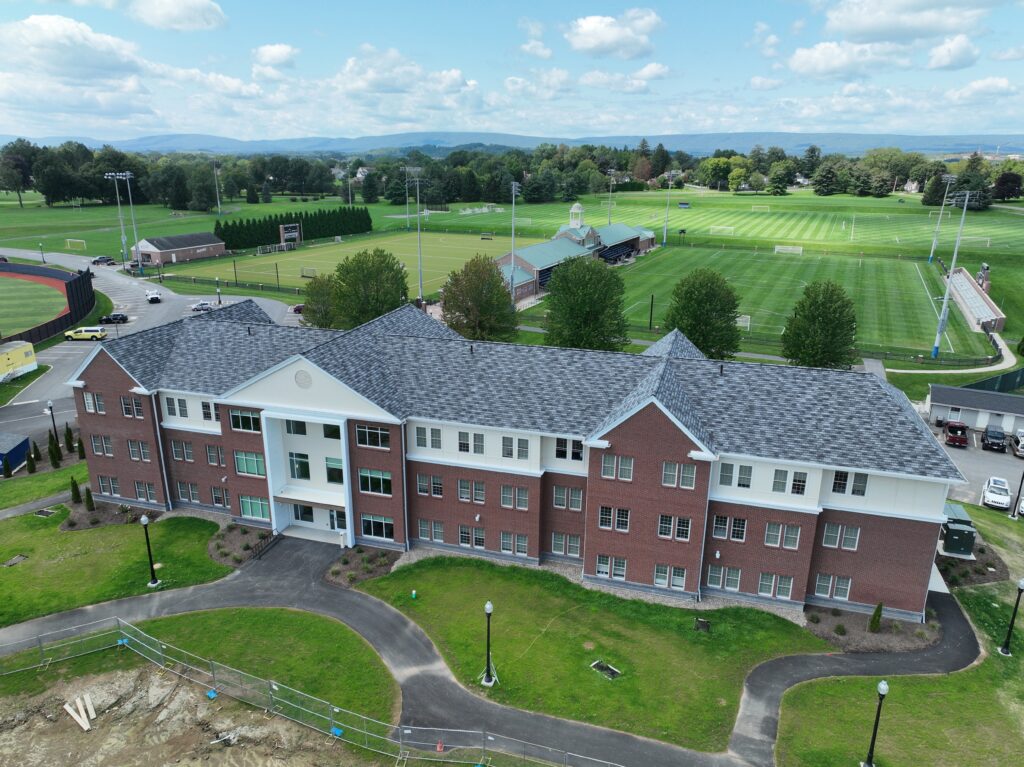