Why Barton Malow went “all in” with Join for Intermountain Health Lutheran Hospital
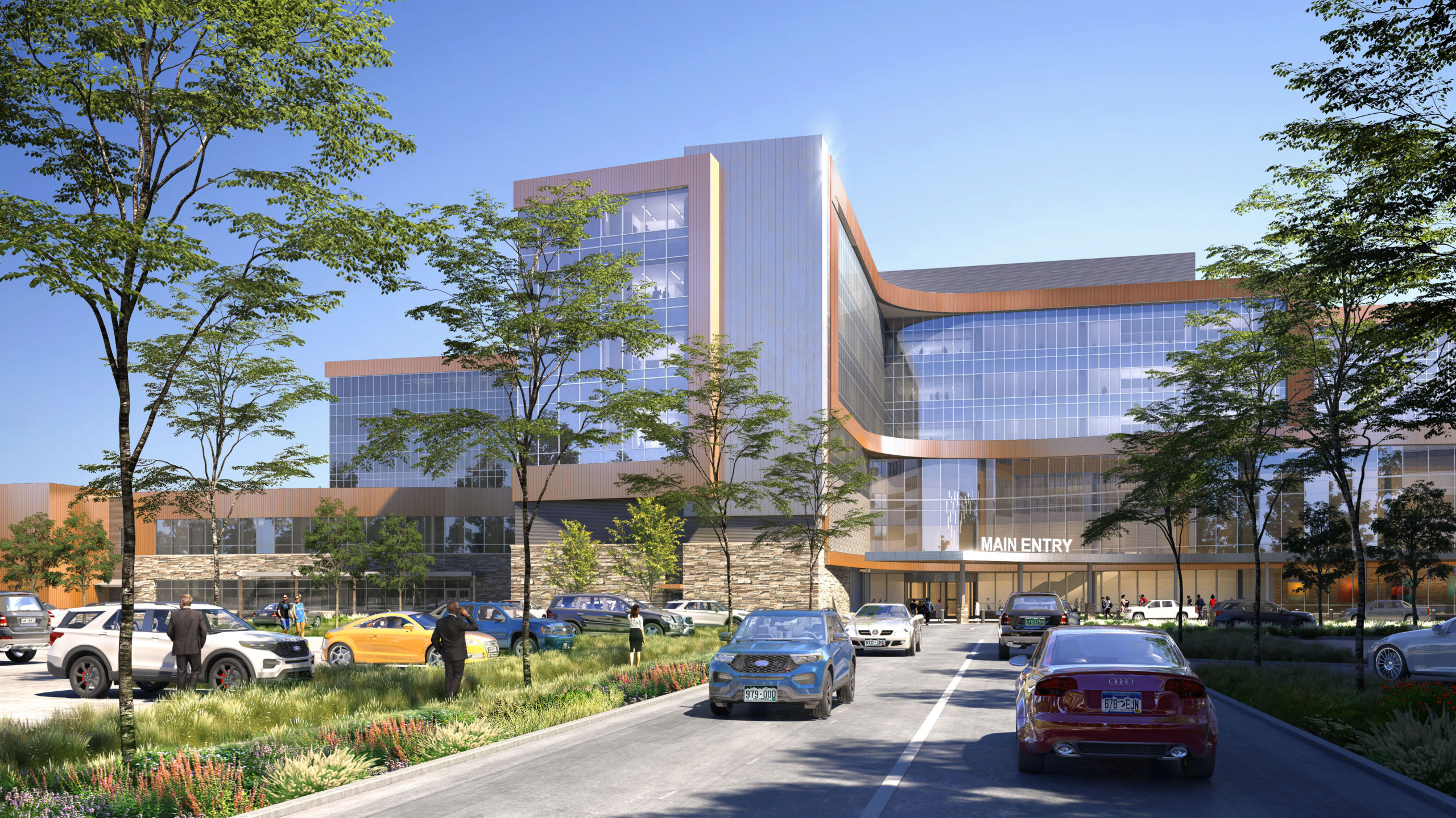
It wasn’t the first time Barton Malow used Join. The company had run a test pilot project with Join during preconstruction for another hospital project. While still relying on Excel, they mirrored their Excel-based processes into Join and compared the experience.
The result was enough to give Barton Malow the confidence they needed to go all in with Join on the SCL Health Lutheran Replacement Hospital (SCL) project, now known as Intermountain Health Lutheran Hospital following the SCL Health-Intermountain Health merger in 2022. The team would abandon Excel and use Join exclusively. Switching to Join was about addressing Excel’s shortcomings
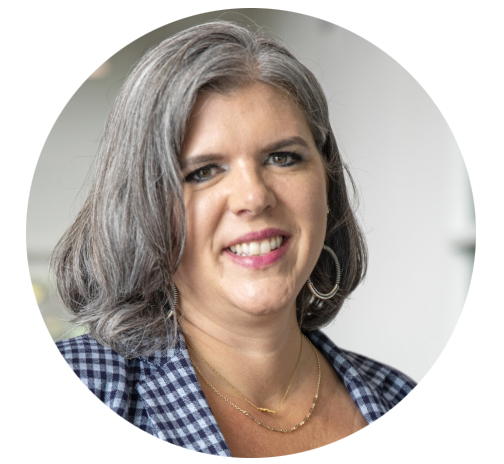
“It’s always a little bit nerve-wracking when you switch. We are dealing with money and very real consequences if the cost tracking tool switch didn’t work. That said, we were confident that Join was the right tool. Join creates transparency for the owner and design team and would create a space to eliminate/reduce surprises at major milestones.”
Vice President of Preconstruction at Barton Malow
From Elizabeth’s perspective, Join addressed four major areas:
Automated vs. manual
Like most construction managers, Barton Malow used Excel during preconstruction. Excel required manual entry when it came to documenting who changed what, when, and why. According to Elizabeth Geiser, Vice President of Preconstruction at Barton Malow, despite there being a comment section in Excel, there wasn’t consistent use by users. All decisions, changes, and reasons had to be manually entered.
With Join, all decisions and changes to items were automatically recorded: who, what, when, and whether or not the user provided reasons and documentation.
Confidence that everyone is oriented around the same data
With Excel, there could only be a single user at any given time, with a static pdf report. The team could never be certain that they were working on or reviewing the latest version.
Join allows for multiple users on a single version that is real-time, therefore maintaining forward progress by eliminating version confusion and backtracking.
Clear definition of what is included in the cost
With Excel solutions, the pricing back-up wasn’t documented consistently (it could be electronic, scrap piece of paper, etc.). There was also no easy way to attach images or documentation to identify what was being priced.
Join allows for estimate detail to be clearly shown, coded, and identified for each item. In Join, anyone on the team can easily attach specs, drawings, and other important data to items.
Visibility into how items impact each other
Excel didn’t account for item relationships. (i.e., that accepting certain items would require acceptance of others or precluded acceptance of others.)
Join makes item relationships readily visible to all users and automatically takes these relationships into account so that calculations follow real-world logic.
Going “all in” with Join: 65 active users
In October 2020, they kicked off preconstruction for SCL. This time, there would be no duplication into Excel. It was “do or die,” said Elizabeth. “It was just like jumping out of the plane and trusting that the parachute was going to work.”
The Barton Malow Haselden team invited not just the people on their team but also the owner, architect, engineers, and trade partners. All the parties were told how the preconstruction team planned to use Join. The team tracked the costs using four custom categorizations (breakout codes) initially and added many more along the way. The expectation was that Join would simplify the tracking of each decision and allow for ease in viewing cost by a number of categories.
Seventy-five people were invited to the project. Sixty-five actively used the platform: 14 users represented the owner’s team, 11 from the design team, 19 represented five key trade partners, and the rest were from the Barton Malow Haselden team.
While some required additional training beyond the one-hour training session, most users became familiar with Join on their own, with many going beyond looking at the project overview. Many leveraged the filters to pivot the data and look at specific items — a process that would have required assistance from the contractor in Excel.
Justin Franklin, Director of the Cumming Group which served as the owner’s rep, previously worked with SCL for six years. He joined Cumming as part of the project and was involved from schematic design and through the entire budgeting process as the drawings and design progressed. He was open to using Join.
Justin used Join regularly to review specific items that needed approval: “Join is great for tracking changes from one milestone to the next and looking at backup documentation.”
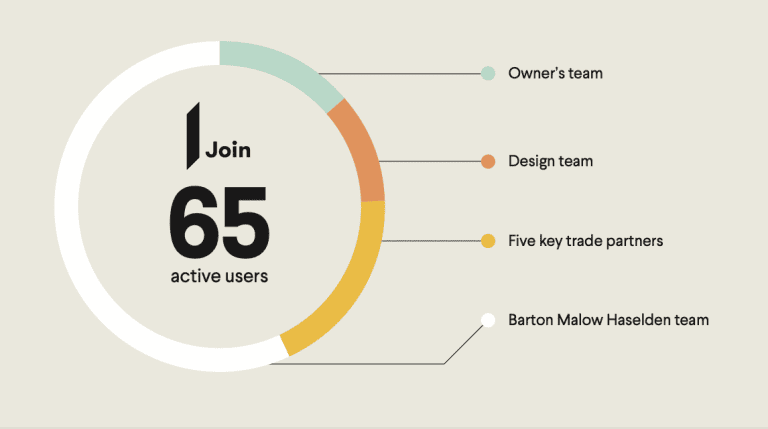
Tracking money and decisions: what Barton Malow learned
The way Elizabeth sees it, Join was not only monitoring cost changes, but was documenting all decisions made throughout the preconstruction process. At any time, those with access could see when a decision was made, who made the decision, why the decision was made, and see any supporting documents attached. As with any change, there were some things the team had to learn together and get comfortable with. The Barton Malow Haselden team had to adapt to the transparency of live updates and tracking of changes the Join platform provides.
Adapting to real-time data
Because Join is always live and automatically updates with every action, the entire team had to learn to temper their reactions. “Sometimes, people got really excited when they’d see six-or seven-digit savings but didn’t realize the added costs were yet to be accounted for,” Elizabeth explained.
To provide clarity and keep people from getting overly excited with cost changes, Barton Malow Haselden added a category to clearly identify item status: “work in progress” or “ready for decision”.
Comments feature for decision tracking
Barton Malow Haselden also learned that it was important to provide clarity on who was accepting and rejecting items. While only a handful of people had the authority to accept or reject items, there were instances when a non-owner accepted a decision, and there needed to be a way to indicate who authorized said decision.
Join’s Comments feature was used to track decisions during and after meetings. People who weren’t present in meetings could also add their comments. Additionally, an additional categorization was created to clearly note the decision maker.
Technology for going lean
Justin, a big proponent of lean processes and technology, says, “I think technology can be a good tool to help facilitate projects. But technology is only as good as the information you put into it.”
During the early stages of the process, there were times when Justin would have liked more detail and backup. But overall, his experience as the owner rep was positive. He sees it as a way to provide a roadmap to budget changes and scope. He likes the historical thread that Join provides – who was making what changes. Having the information all in one place available anywhere anytime was a game changer.
Trust, collaboration, understanding, and the end of reports
In the end, according to Elizabeth, everything comes down to money. Join, in her view, helps build trust by providing the understanding and transparency needed to ensure the owner that the Barton Malow Haselden team wasn’t playing games. It was particularly important during instances when what looked like big savings didn’t show up in the final calculations. She feels that Join provided the neutral space that allowed true collaboration: trade partners could enter their own pricing, the design team had a platform to drop in images as needed to provide clarity, and at any time anyone on the team could add a comment or search key words to find the history of an item. It was this true collaboration that helped build trust.
“Join put everyone on the same page with the different decisions. Whether it was an owner change, a VE item, or a design change, Join made it easier to build consensus to approve or reject the item and let the team know they could move forward.”
— Elizabeth Geiser, Vice President of Preconstruction at Barton Malow
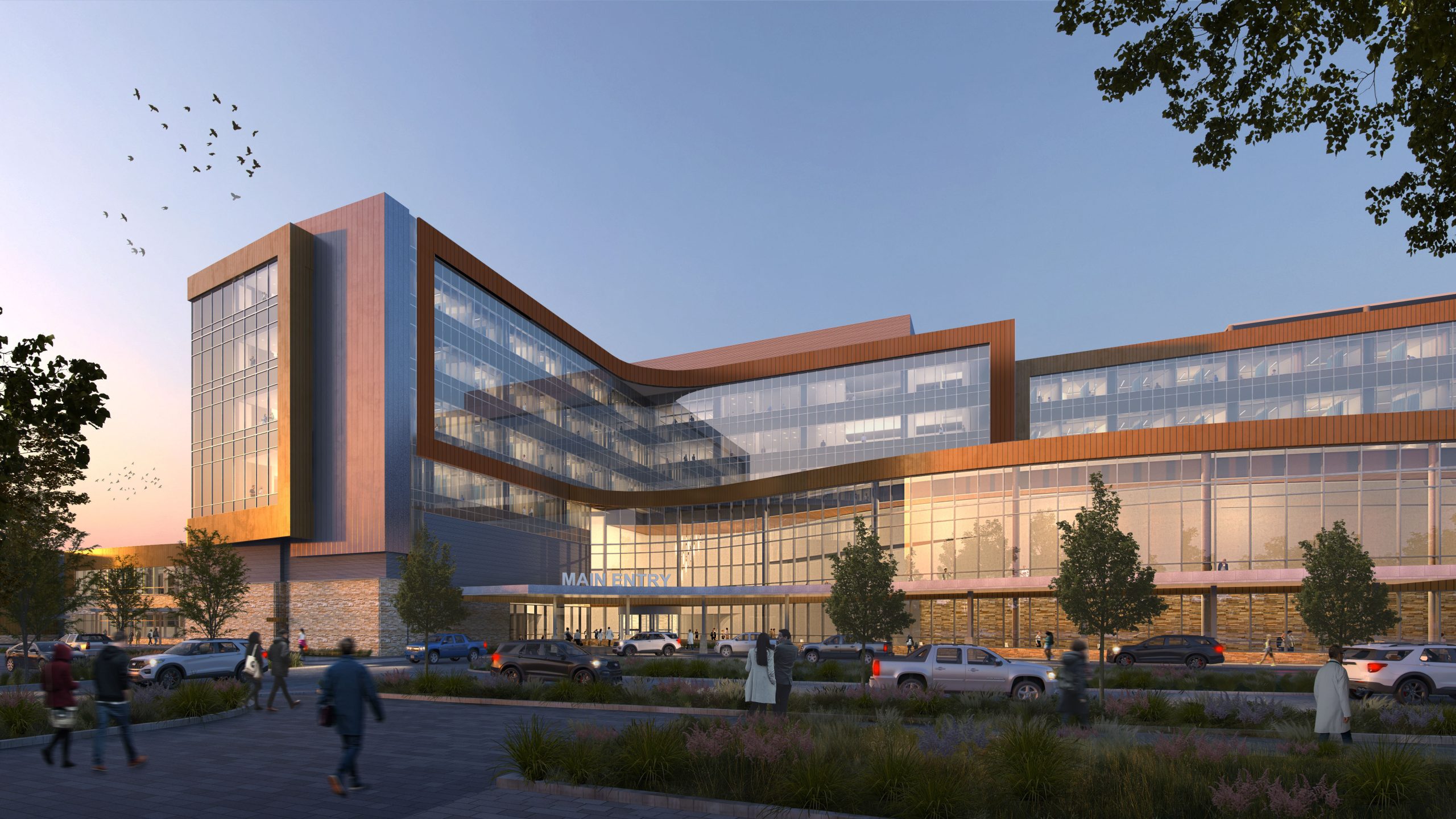
Intuitive platform
Andrew Schwabe was the project manager within HDR, Inc., working withall the consultants from MEP to project architects and designers. He had never used anything quite like Join, so he didn’t have a lot of confidence in or understanding of its accuracy or how things would be updated. But he trusted the team, and as time went on, Join’s usefulness became clear. “It was pretty nice to have something that you could immediately reference to see the budget status, and have it updated in real-time,” he said.
Streamlined communication
Email exchanges were dramatically reduced. And since everyone involved in the preconstruction phase had access to Join, Barton Malow Haselden never had to produce any reports. “The team could go into the system, look at what they wanted to see – anytime,” said Elizabeth.
Justin agreed. “Executive owners care most about the bottom line and shouldn’t have to wade through mountains of complex data and reports to get to it.”
Goal-driven, productive meetings
Meeting preparation was never easier, according to Neal Wondel of Cator, Ruma, & Associates. Neal was the electrical and project manager in charge. “I could actually prepare for meetings,” he said. “Before Join, a typical meeting would be spent gathering information, trying to find the information on a 100- page spreadsheet, and then you’d go away to process.” With Join, he said, he’d have all the information he needed beforehand, which served as the basis for discussion, and maybe for additional fact-finding.
“We could spend our meetings reviewing cost and opportunities. Having all the documentation in one place was really nice, and it was great to be able to pull up an item and talk through the decision.”
Real-time budget clarity
While the budget went up and down based on the changes being made, the team achieved the project’s budget goals.
“We were able to show the broader team the same budget with the same updates. Join also allowed documented the history of the project. There was a desire to be lean and find cost savings while also maintaining the standards of St. Joe’s (another hospital project by the same owner). Join allowed for clear tracking of cost if the owner wanted to match St. Joe and/or other benchmark projects. This allowed the team to analyze premium costs for this project?” According to Andrew, these are the types of discussions that Join made possible. He now says he’d recommend using Join for other projects.
“Once a team has experience using Join, it’s easy to use it on any project type and size,” he said.
Decision history
James Dickerson of Cator, Ruma, & Assoc. was the mechanical engineer of record on the project, the head of the team that gets sued “if the bridge falls down.” He signed all the drawings, so for him, the central repository of content, the permanent record of who made the decisions and when was the greatest value of Join.
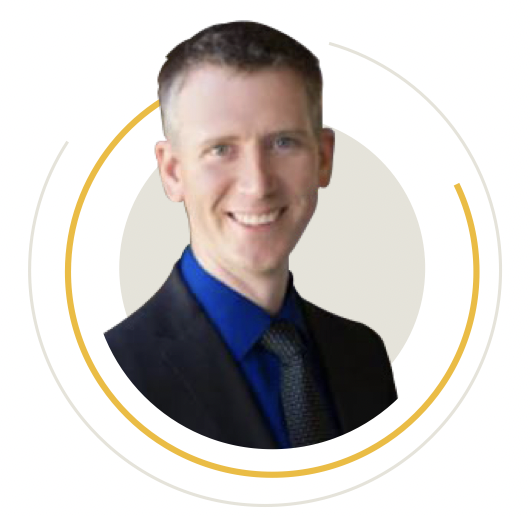
“Before Join, a typical meeting would be spent gathering information, trying to find the information on a 100-page spreadsheet… [with Join] we could spend our meetings reviewing cost and opportunities.”
Principal/Electrical Engineer at Cator, Ruma, & Associates
Goodbye Excel
Join is now integral to Barton Malow’s preconstruction process
With SCL, Join has now been used for 16 of Barton Malow’s projects. Join has become integral to Barton Malow Builders’ preconstruction process – the side of the business that works on hospitals, higher education, K-12, mixed use, and other commercial projects.
“We like the transparency, the live updates, and the ability to view from anywhere,” said Elizabeth. “The sorting capabilities can mirror the way we do estimating, resulting in no additional time coding/tracking items. Our preconstruction team also likes that we can go in and see estimate detail, attachments and decision documentation at any phase of the process.”