The Future of Supply Chains and VE Post COVID19
Pre COVID-19, it wasn’t uncommon to have a few folks working in remote locations during project meetings, but now and for the foreseeable future, we’ll all be collaborating virtually all the time. This makes it especially hard to have quick and productive ad-hoc interactions with our coworkers and project teams, and forces us to take a hard look at the project collaborative processes we’ve used in the past and re-evaluate their effectiveness in this new normal.
This is especially true when it comes to processes like value engineering (VE) and how we deal with the product supply chain. When we’re looking at options that might have cost, schedule, or performance implications, they often will directly or indirectly involve products or materials which can have many potentially unknown logistical challenges.
One big challenge is that product and material expertise is usually several degrees of separation removed from our traditional VE collaborative process. Especially now, in a COVID-19 world, we have to address this to ensure any decisions we make around products and materials are informed and actionable.
VE isn’t Just About Cost-Cutting: it’s Also Products and Materials
Generally attributed to Lawrence Miles, Jerry Leftow, and Harry Erlicher at General Electric Co. during World War II, value engineering emerged as a strategy to address shortages in skilled labor, raw materials, and manufactured parts. Today, every construction project practices some form of value engineering, whether called so explicitly or not. To many in the construction industry, it’s become commonly believed that VE is only about cost reduction.
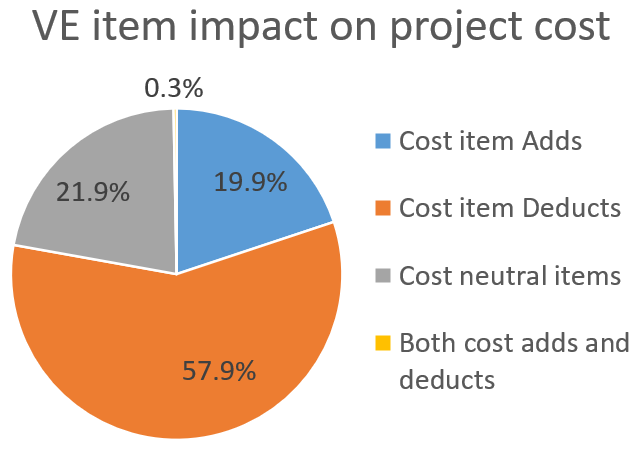
The VE item impact on project cost chart above shows the project cost impact of value engineering done during the preconstruction phase of negotiated bid projects. These data come from an evaluation across several dozen unique projects at different phases of preconstruction, ranging from healthcare to wastewater projects in different geographical regions across the US.
While it’s interesting to note that nearly 58% of VE items result in a project cost deduct, nearly 41% of VE items are either cost-neutral or increase overall project cost.
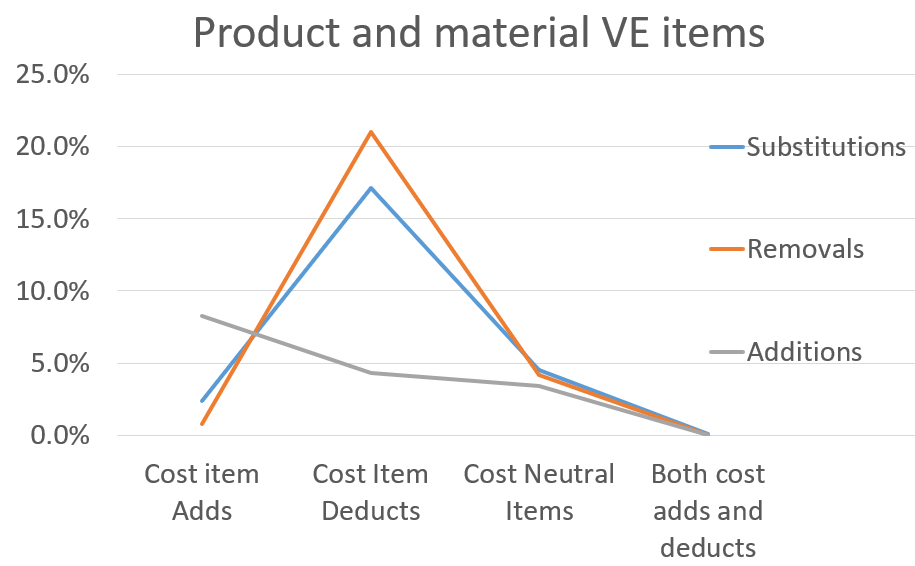
How do these data break down in terms of their relation to the supply chain? Further analysis shows that 24% of VE items are directly related to a product or material substitution for various reasons. Similarly, over 42% of VE items are either directly or indirectly involved in adding or removing product or material scopes. Combined, over 66% of VE items under consideration affect products and materials.
Is our supply chain under pressure?
There have been numerous articles recently detailing supply chain impacts as the current pandemic has unfolded and become a persistent reality.
Even before today’s pandemic, we faced a dire shortage of skilled labor for our projects and factory workers. There are many supply-chain disruptions that are going to be accelerated by the impacts of COVID-19 as we search for more safe working conditions around project assembly.
This includes many general contractors moving quickly towards offsite fabrication where they can have greater control over working conditions, product quality, bulk purchasing power and cost. In fact, McKinsey addresses multiple aspects of this in it’s June 2020 study: “The next normal in construction”.
But assembly improvements put even greater demand on how materials and products are sourced for a project. Rapid demand for certain types of construction in today’s COVID-19 market (e.g., critical infrastructure, medical care facilities, etc. vs. office space, hospitality, etc.) will put ever more emphasis on a local-first approach to how products and materials are secured, produced and delivered.
To meet this demand, innovation will come from both existing producers with their current distribution models and from new vendors entering the market without legacy infrastructure. Everyone agrees that trade and self-perform contractors need to be diversifying their portfolio of suppliers to ensure the availability of critical products and materials.
This is possible with existing vendor relationships, but much more challenging when it comes to emerging products and materials from vendors and suppliers that they may be yet unaware of. For decision-makers to fairly evaluate their VE options, they’ll need current and relevant access to the related supply-side dynamics to even have the chance to make a more informed decision.
This is where a much deeper level of preconstruction collaboration is critical. Trade contractors and potential product specialists need to be directly involved in helping inform a critical VE decision that pertains to their subject matter expertise. This allows decision-makers the chance to ask the necessary questions to fully vet product and material-related options that will have a long-term impact on the suitability and sustainability of their project.
Are Old Technologies Getting in Our Way?
A side-effect of globalization is that we’re all now used to working with people across multiple time-zones and geographies.
Many of us will also continue to work from our homes and be less dependent on our offices. The opportunity to have quick conversations with peers and project colleagues is even more critical than ever, and having greater transparency for collaboration is fundamental to project success. Technology has to make this possible at every step. Otherwise it’s going to continue the path of siloed information that’s inaccessible when needed most.
As a fully collaborative hosted solution, Join, for example, allows all project team members to come together to digitally discuss a critical decision. Given the uncertainty and opportunities around products and materials, this type of collaborative environment is even more essential in these challenging times to successfully get our projects built to cost and schedule.
If you’re interested in how Join may be able to help solve these challenges, give us a shout.